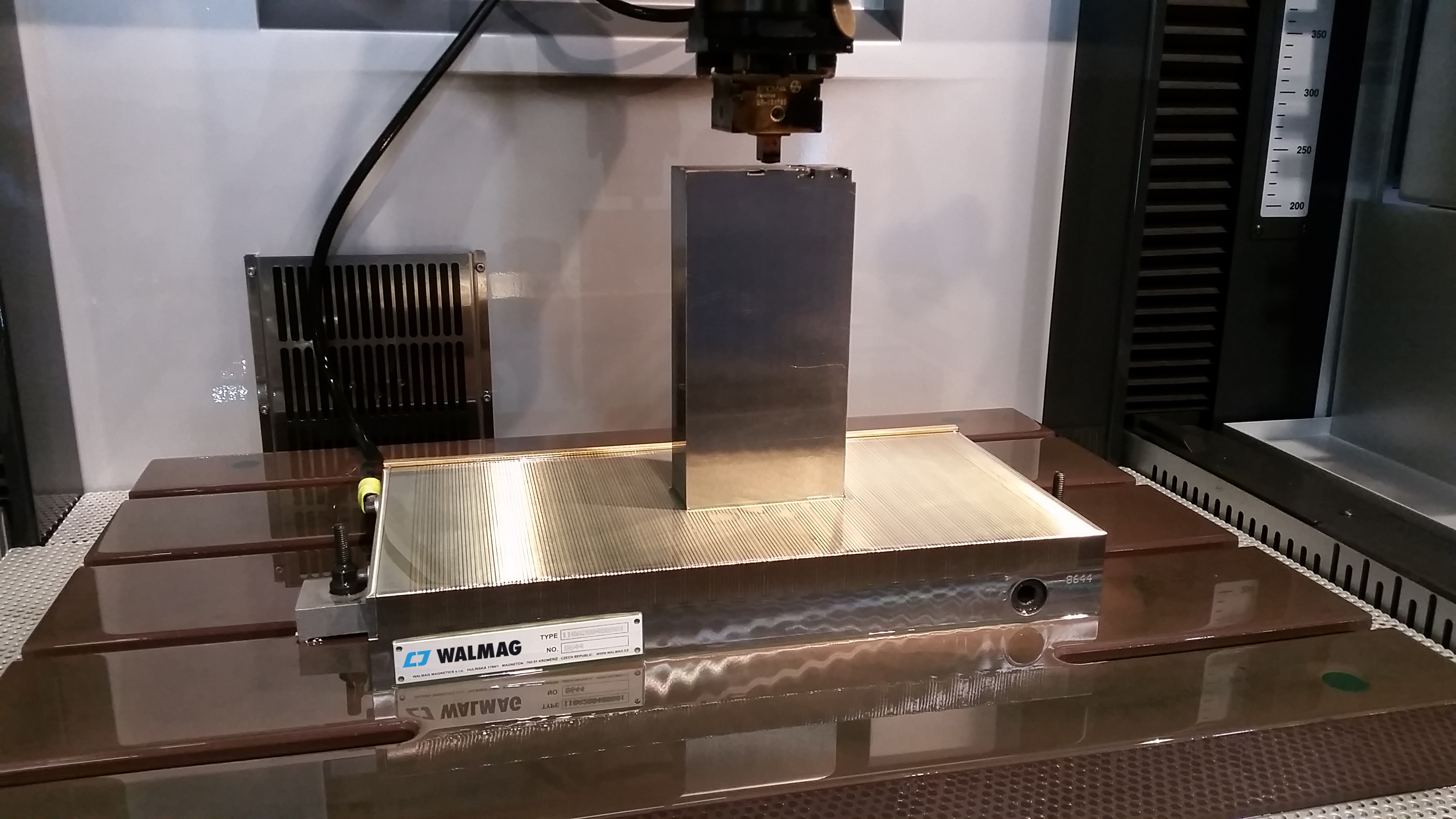
Clamping force of magnets is the highest when clamping
larger and even workpieces.
Workpieces from ferromagnetic materials can be clamped by magnets during the machining process. To achieve the maximal clamping force and fully use the benefits of clamping with a magnet, you need to consider the material type and thickness of your workpiece, its temperature or size of the contact surface.
Type of material
The lines of magnetic flux pass the best through low carbon steel, such as C15 or C22, with carbon content of approximately 0.15%. Good news—this type of steel is the most commonly used one in the metal industry.
On the contrary, high carbon steel and alloy steel contain more non-magnetic elements which impede the passing of magnetic flux through them. To put this into perspective: The ability of magnetic flux lines to pass through cast iron (alloy of iron and carbon with the carbon content being over 2.14%) is reduced approximately to a half when compared to low carbon steel.
Thickness of material
If the dimensions of a workpiece are not larger than 3 mm in height and 200 mm2 in surface area, the magnetic field can pass through the material and close itself just above the workpiece, which lowers the magnetic force as well as the clamping force due to the contact surface not being large enough. In such cases, not all lines of the magnetic flux pass through the workpieces—some may form around the workpiece and therefore not contribute to full clamping force.
As a result, magnetic clamping of very small or thin workpieces is suitable for light machining where the pressure of the worktool on the workpiece is not as high.
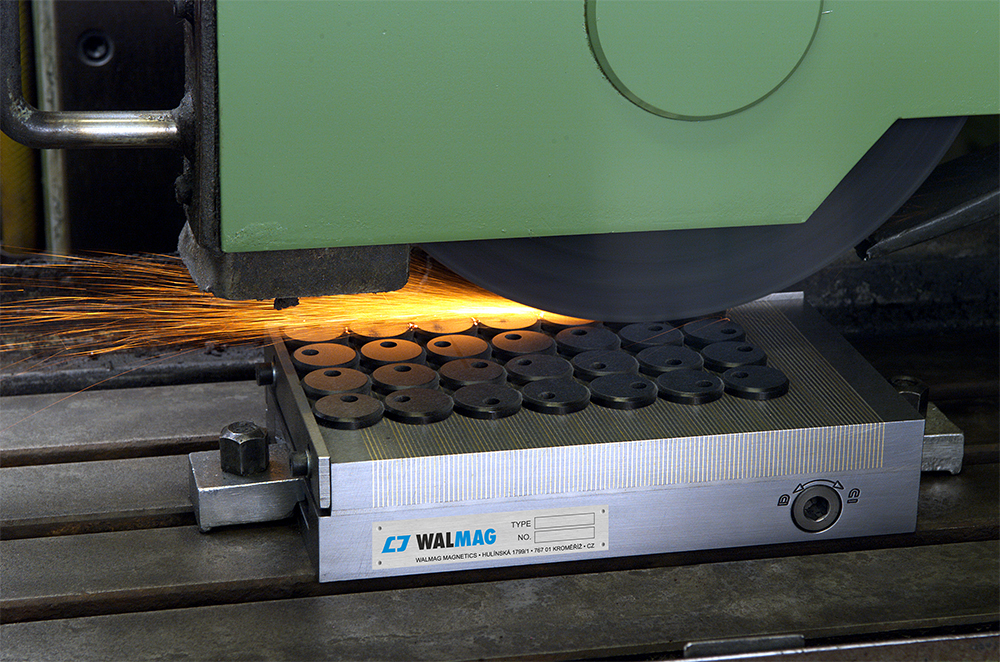
Clamp multiple smaller workpieces at once to increase
the work efficiency as well as the clamping force
of the magnet.
Air capsule
Dirt (such as paint remains or rust) and air capsules are the worst enemies of magnetic force as they don’t allow for the magnetic flux lines to pass through, thus decreasing the magnetic force. A 0.5 mm air capsule can decrease a magnet’s force by 80%! For this reason, magnet manufacturers always recommend to maintain the magnet as well as the clamped workpiece clean, smooth, and if possible, even.
Make the work easier for your magnets and try to provide the largest and cleanest contact surface as possible, as well as a clean and dust-free workspace.
Contact surface
To achieve the maximal clamping force of a magnet, a workpiece should completely cover both north and south poles of the clamping magnet. A smaller workpiece should at least cover the north and south poles evenly, even if only partially. This will help you achieve the best possible clamping force in such a situation.
In practice, multiple smaller workpieces are clamped on a workdesk, thus closing the circuit between the north and south pole. This makes the magnetic flux more efficient and consequently maximises the magnetic force.
Temperature
Permanent magnets have a negative temperature coefficient, which means that their magnetic force decreases at high temperatures. For example, just 50 °C lowers the clamping force of a magnet by 10%. That’s why we recommend cooling down the magnet with water during machining, which also helps with smooth removal of metal chips and sparks. Some manufacturers offer magnets with a special surface, composed of materials that make them more resistant to higher temperatures.
Considering the purchase of magnetic tools for your production? We’d be more than happy to help you—contact us!