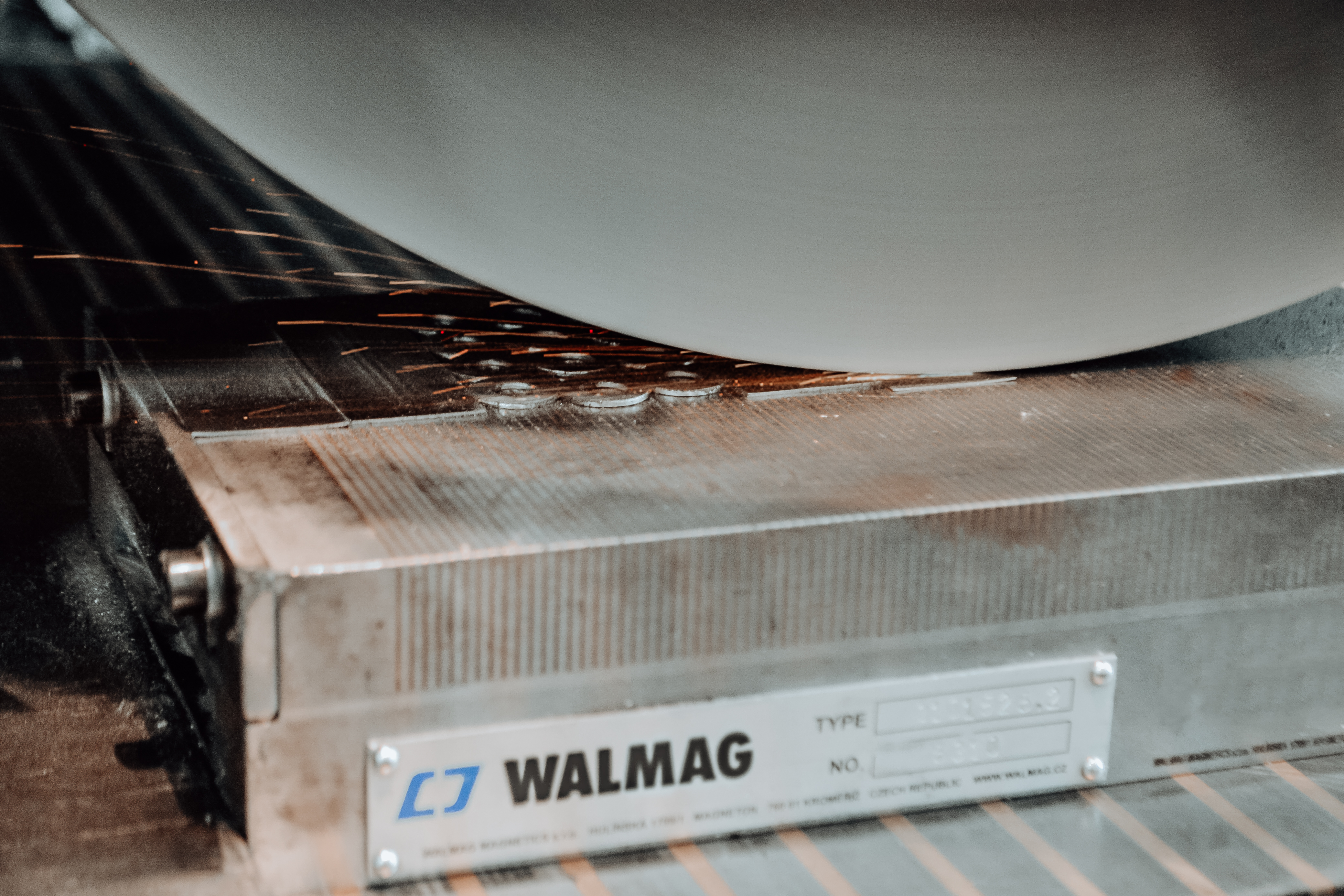
A magnet can clamp several workpieces at once, this
making use of the entire surface of the workstation
How to clamp small or fragile workpieces during machining? You need a tool that will help you attach workpieces to your workstation firmly and securely—they shouldn’t move or get damaged during machining. The most suitable tools would be magnets, vacuum clamps, and freeze clamping. How do these differ?
Mechanical Clamping: Limited by size
Only workpieces sufficient in size can be clamped by mechanical clamps or chucks. Moreover, workpieces need to be sufficiently firm; if they’re not, mechanical clamps might damage them.
If you’re using mechanical clamps for thin, small or fragile workpieces, we recommend using multi-jaw chucks in order to distribute the pressure. For better protection against damaging the workpiece, look for clamps or chucks with plastic or aluminium coating on their jaws—these materials make them softer. Or use clamping plates to attach thin, small or fragile workpieces to your workstation.
Magnetic Clamping: Ideal for the most fragile workpieces
Magnetic clamping is ideal for the most fragile workpieces as there’s zero risk of damaging the clamped workpiece. However, there’s a workpiece size limit: Magnetic field permeates the material of workpieces smaller than 3 mm in height and with a surface area below 200 mm2, then closes itself above the clamped workpiece. Because of this phenomenon, you can’t clamp the smallest workpieces with a magnet due to the contact area being too small—this could only work for light machining (such as finish sanding with low output).
Workpieces thicker than 3 mm or bigger than 200 mm2 in size are much more suitable for magnetic clamping as they can be firmly clamped. For these, magnetic clamping works well even for heavy machining.
Vacuum clamps: Suitable for non-magnetic materials
Vacuum clamps are a suitable alternative to magnetic clamping for non-magnetic materials—like wood, aluminium, stainless steel or brass. A vacuum pump suctions air under the clamped workpiece, thus decreasing air pressure under the workpiece, making the surrounding (higher) air pressure firmly attach the workpiece to the workstation.
In comparison with magnetic clamping, vacuum clamps are weaker and cannot be used for porous or perforated workpieces.
Freeze clamping or adhesive workholding systems
Another tool for clamping thin, small or fragile workpieces would be freeze clamping. A freeze clamping device covers the surface of the clamped workpiece with a water film which it then rapidly freezes, thus attaching the workpiece to the workstation. Most commonly, freeze clamping is used by jewellery or watch manufacturers. Generally, freeze clamping is suitable for smaller productions as it’s relatively expensive and technologically demanding.
Some companies use clamping by glue—the workpiece is anchored to the workstation with a special adhesive mold that is removed by heat once machining is completed. This is an effective workholding method; however, similarly to freeze clamping, it’s not well suited for mass production.
When choosing the optimal technology for clamping, we recommend keeping in mind the amount or time needed to clamp a workpiece or the serial nature of your production. For example, you can clamp the workpieces on the entire surface of your workstation with magnetic clamps/chucks, which makes the production significantly faster in the long run.
Do you feel like you could use some guidance when choosing the right clamping technology? Contact us and we’ll be happy to provide assistance.