
Clamping a workpiece with a magnetic chuck is easier than manual clamping.
Lifting or securing workpieces by magnets is less demanding than clamping or lifting workpieces manually. In most cases, the only thing the operator needs to do is to read the enclosed user manual thoroughly. Only more robust magnetic sets might be an exception to this rule. For those, we provide staff training and phone consultations at Walmag.
Operation of Magnetic Chucks
Magnetic chucks are used to securely clamp a workpiece to the work station for following machining operations — the operator only needs to respect general rules of safe clamping. It takes seconds or just a few minutes to secure a workpiece with a magnetic chuck; what matters the most is setting the clamped workpiece in the correct position on the workstation and maintaining the optimal angle towards the machining device. Then the operator just presses a button or switches a lever to activate the magnet.
With a magnetic chuck, the clamped workpiece is easily accessible from five sides and there’s no need to re-clamp the workpiece repeatedly during machining. This speeds up the entire machining process and eliminates the risk of a mistake caused by loose clamping. We can say with confidence that magnetic clamping is 8× faster than clamping a workpiece manually.
When done with machining, the operator simply deactivates the magnet and removes the workpiece from the workstation. Supposing everything works well, the workpiece gets demagnetised automatically at the time of switching off the magnetic chuck. That said, you can always run the demagnetisation process manually.
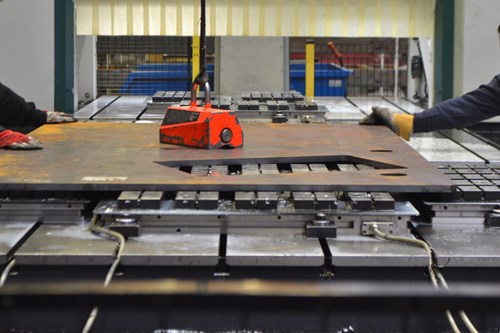
Operation of Lifting Magnets
When compared to securing a lifted workpiece manually, not only is lifting a workpiece by a lifting magnet much quicker, it’s also a lot safer. Employees don’t need to put their hands under the lifted workpiece, let alone enter the space under it — thus entirely avoiding accidents in this potentially high-risk area. The only task the operator really has to focus on is centering the magnet on the workpiece and then activating the lifting magnet by a switch lever or pressing a button.
Crane operators need to have a special lifting permit to lift heavier workpieces — but this requirement applies for manual lifting, too. When operating a crane with a lifting magnet, the crane operator needs to centre the magnet on the workpiece and then activate the magnet by switching a lever or pressing a button. The only concern is the maximum lifting capacity of the magnet which always has to be respected.
Special Training Required Only Exceptionally
We have plenty of experience with supplying magnets to production facilities or warehouses. Mostly, the staff only need to read the user manual to operate the magnets safely or may need to discuss the use with their magnet supplier. Staff with no previous experience might have safety concerns due to the fact that the magnetic force cannot be seen. These worries usually dissolve within a few days.
When supplying a more robust set of magnets, we provide short staff training in magnet operation. Very often, this proves to be unnecessary and we just provide user support over the phone.
Hopefully, you’re now familiar with the use of magnetic chucks and lifting magnets and know it’s nothing you (or your staff) should worry about. Magnet operation is simple, quick and comfortable and the result is absolutely safe. In case you want to test out Walmag magnets before committing to them, contact us! We’d be happy to lend magnets to you at first.