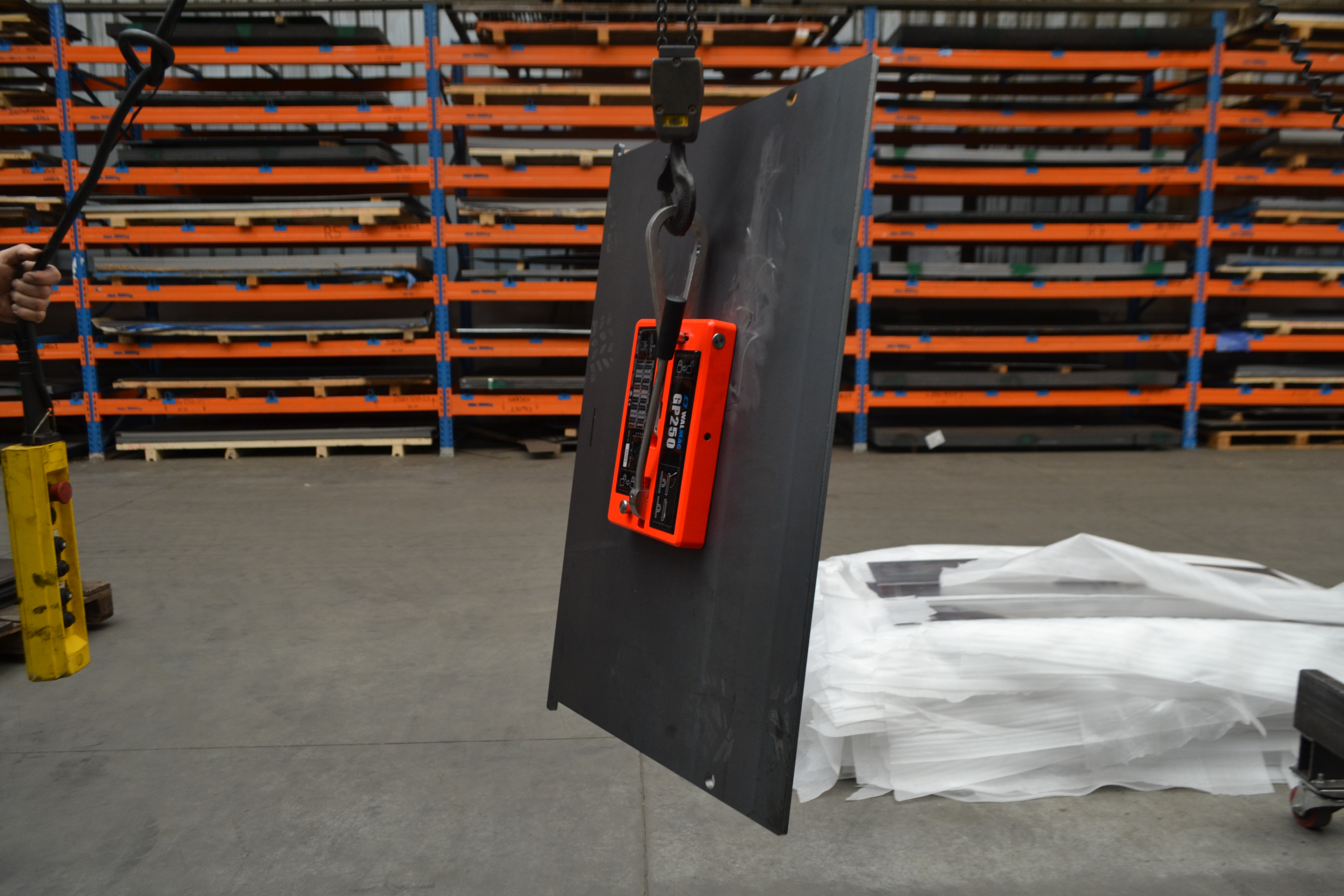
Choosing the right magnet makes sure the metal sheet
doesn't slip by itself
Handling metal sheets brings a number of complications—sheets bend, are prone to damage and there’s always a high risk of injury hanging above the operator’s head. In most cases, the most efficient way to handle steel sheets is to lift them with lifting magnets or with vacuum manipulators. Mechanical fixation (lifting clamps) is considered outdated and not suitable for thin metal sheets.
Mechanical clamps: not suitable for metal sheets
- Mechanical clamps can damage the structure of thin sheets
- They can slip uncontrollably
- They always require extra space under the sheet (stacked sheets need to be separated manually).
There’s always a safety risk for the operator when lifting metal sheets mechanically, increased by the fact that mechanical clamping requires manual handling of the clamp and the metal sheet. Metal sheets need to be attached to hooks or chains by hand which makes manual clamping considerably slower. With lifting magnets or vacuum manipulators, no manual handling is necessary.
Another limit of mechanical clamps would be the required minimal thickness of the clamped sheet—a requirement that is often not met. Lifting magnets and vacuum lifters can easily handle metal sheets at least 3 mm thick which is the minimal thickness of most steel sheets.
Benefits of magnetic handling of metal sheets
A lifting magnet can magnetize multiple metal sheets at once. To be sure your magnetic lifter is capable of this, don’t forget to carefully check its parameters (especially the lifting force of the magnet and the maximal measurements of the lifted object). We recommend choosing a BM battery magnet with a load test function. This function allows the magnet to decrease its lifting force shortly after magnetizing and the initial lift of multiple sheets. That causes the sheets on the bottom (held by lower magnetic force) to fall off; the magnet then increases its lifting force back to 100% and continues to lift the optimal number of sheets that will safely adhere to it.
Battery-powered BM magnets can also drop the bottom sheets if necessary. This is called the Tip-Off function. It decreases the magnetic field under the magnet, thus releasing the material at the very bottom.
How to tackle bending of metal sheets
To prevent metal sheets from bending when handled, we recommend following these rules:
- never use magnets to handle metal sheets thinner than 3 mm—the magnetic force would simply pass through them and would not attach them firmly; very thin metal sheets also tend to bend and peel
- make sure to handle metal sheets of the correct dimensions and weight, following the manufacturer’s manual (for a 3 mm sheet, the usual maximum dimensions to be handled by a magnet would be 2.8 m x 1.8 m with maximum weight of 110 kg).
If you need to handle larger metal sheets, we recommend using more lifting magnets. Oftentimes, a more robust system using mains operated electromagnets of higher power, backed-up by batteries, needs to be installed. Another way to handle metal sheets of large dimensions would be to build a powerful electropermanent magnetic system.
When handling metal sheets thinner than 3 mm on a regular basis, we recommend getting a vacuum manipulator with suction cups placed on the entire surface of the sheet.
In case you work with smaller metal sheets, magnetic lifting is simply the best solution. Apart from the aforementioned benefits, magnetic lifting is:
- less demanding maintenance-wise (suction cups of vacuum lifters wear off more quickly)
- less sensitive to dust and dents (dust decreases the lifting power of a magnet but represents even a bigger obstacle for vacuum manipulators)
- able to lift multiple sheets at once, contrary to vacuum lifters.
Do you want to learn more about lifting magnets in production, or are you considering borrowing a magnet to try it out? Feel free to contact us!